I'd be grateful if you could give me criticism and advice as the process advances as I'm neither a chippy or a shaper so there are bound to be times when its obvious to eveyone but me that I'm screwing up!
Before I start, credit where credit is due: Paul Jensen on swaylocks (who at least) revived the hollow wood surfboard (check out hollowsurfboards.com)... and Daniel Hess who has refined the concept to make the boards contemporary (www.hesssurfboards.com). These are all their ideas that I've nicked.
So here's stage one. The planshape is a slightly stretched (5'8") version of the liss fish in the surfboard design and construction book. The finished board will be (approx) 5'8" x 22 1/4" x 2 1/2"
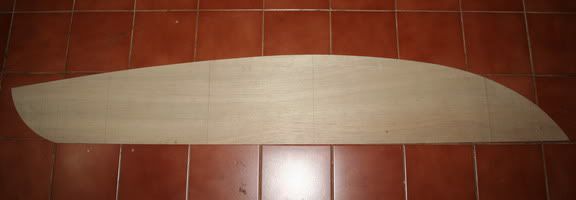
I'm going to start by building the rails and working inwards from there.
My first hws was really heavy, about 8kgs (!) and almost all this weight was in the rails (the rail bands were 1 1/2" thick and corky shape). The new rails will be built up out of 8 x 1/8" strips of wood, so the rail band will be only 1" thick. I'm also going to roll the deck alot so I can get the rails thinner. I hope this doesn't affect the characteristics of the fish negatively.
To make the rails, first I've made a glueup jig, which is basically the planshape of the fish minus 1". I've cut the outline onto two pieces of 1/4" ply and glued the two pieces together with 8" spacers between them to make a kind of box:
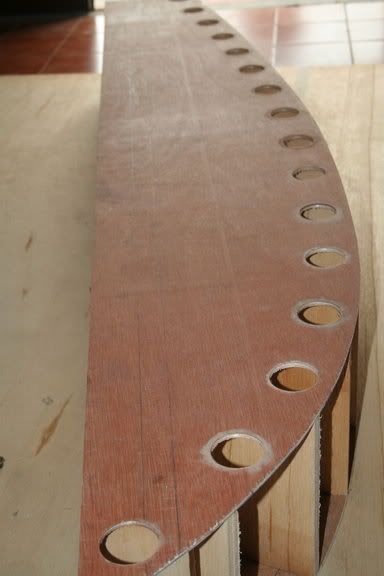
You can see I've cut holes into the sides to locate the (many many) clamps that will be needed during the rail glueup. The ply is only thin so I've also glued some pvc pipe through the clamp holes to try and protect the jig from the clamps jaws.
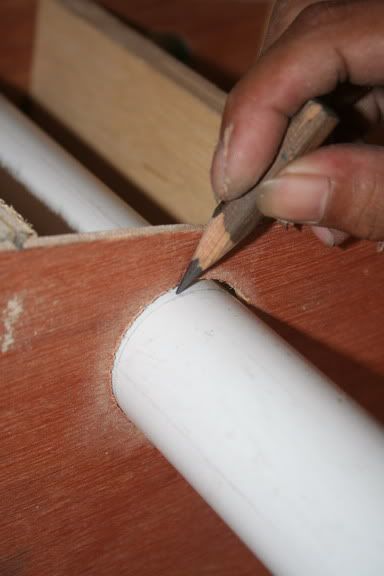
That's it so far.
I hope this isn't out of place in this forum or on this site. Seeing as it's going to be a kneeboard I thought I'd get more appropriate feedback here than on other sites. Maybe it will be interesting to some people. Feel free to tell me if I'm wrong!
Cheers,
Tom